- HOME
- Production Process
- Precision Products
Production Process〈Precision Products〉
Using silica glass, we can assemble a single product by welding or fusing numerous parts together. For products with more complicated structures, however, the process also becomes more complicated. Here, we introduce a typical process for creating a precision product up through its completion.
NOTE: We have left out a thermal treatment called “annealing”, which removes damage caused to silica glass as a result of processing distortion.
1Selection of Material
2Cutting/Slicing
3Grinding/Machining
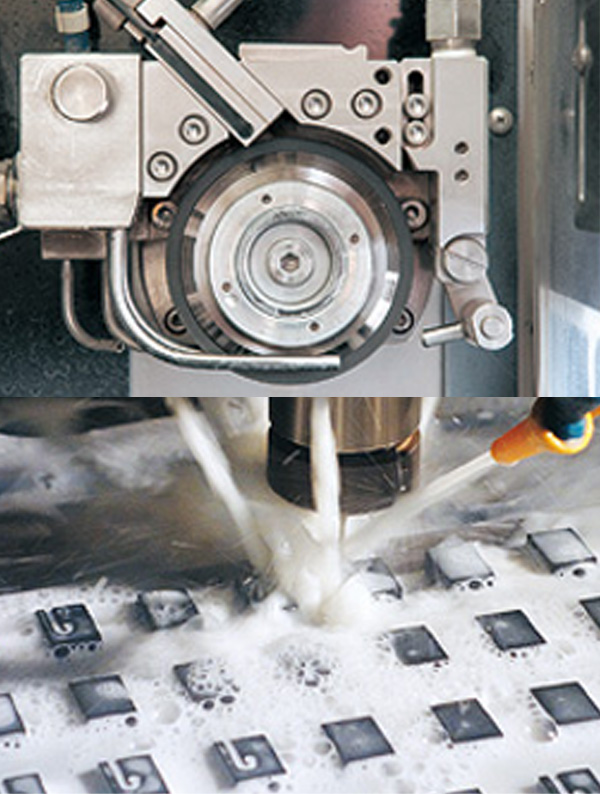
Grinding and machining are processes for fabricating product materials and creating product shapes. Our company has its own precision grinding technology, including a process for drilling small diameter holes using machining centers and laser cutting machines. We create our products by selecting and combining the most suitable processing methods and processing machinery depending on the required level of accuracy and quality.
Flow cytometry cells (flow cells used for hematology/urinalysis analyzers) are another one of our major business lines. We are now mass producing such cells using a special image-processing grinding system.
Comparison of Small Hole Drilling
Method | Minimum Size(mm) | Accuracy(mm) | Notes |
---|---|---|---|
Machining Center | Φ0.3 | 0.02 | |
Laser Beam Machine | Φ0.3 | 0.05 | Developing φ0.01 mm |
Ultrasonic Machining | Φ0.5 | 0.05 |
Typical values. Product specifications can be adjusted according to proposals.
4Polishing
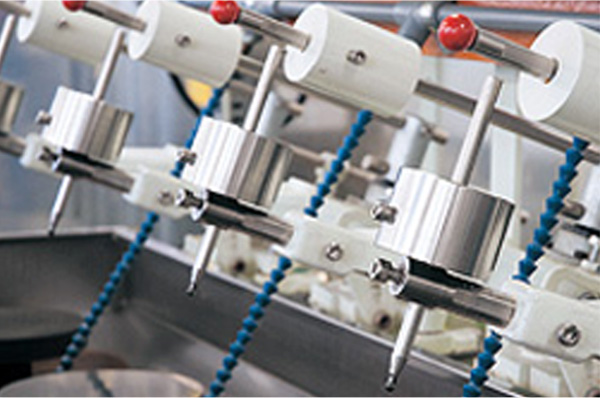
We selectively use various kinds of polishing machines depending on the product’s size and required specifications, including double-sided polishing machines for polishing substrates and one-sided polishing machines for polishing structures and small-volume products.
Light transmission defect standards are becoming stricter every year for flow cells mounted on increasingly high-precision, high-resolution diagnosis/analytical instruments because customers require highly flat polished surfaces with little or no defects. Improved polishing technology is also essential in order to improve the quality of the bond. Our company is working to improve our polishing technology by promoting national certification for our polishing technicians.
Comparison of Polishing Methods
Method | Maximum Work Size(mm) | Polishing Medium(Final) | Surface Roughness Ra(nm) |
---|---|---|---|
Small Single-sided Polish | Φ200 | Cerium Oxide | 0.5 |
Large Single-sided Polish | Φ1,000 | Cerium Oxide | 0.1 |
Double-sided Polish | Φ400 | Cerium Oxide | 0.3 |
Colloidal Silica | 0.1 |
Typical values. Product specifications can be adjusted according to proposals.
5Channeling/Grooving
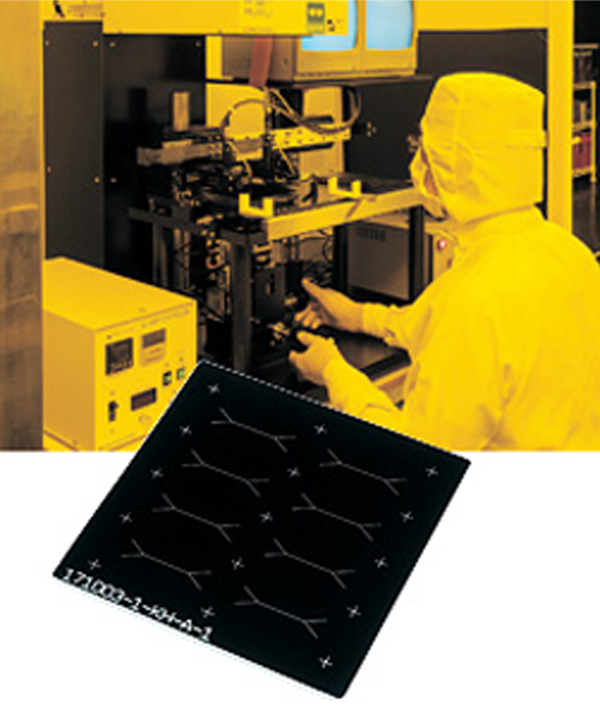
Flow channels in optical flow cells are typically formed by fusing polished parts to each other. This method is effective for forming linear flow channels, but is not adequate for creating complex flow channels. Our company is creating products with minute and complex flow channel constructions, including microfluidic chips, by using the same lithography and etching technologies that are used for manufacturing semiconductors.
We are also able to form channels/grooves using grinding machines such as machining centers, dicing saws, etc.
Comparison of Channeling/Grooving Methods
Method | Channel Width(mm) | Channel Roughness Ra(nm) | Available Pattern |
---|---|---|---|
Thermal Fusion | ≧0.05 | 0.5 | Straight |
Lithograph & Etching | ≧0.002 | 1 | Flexible |
Machining Center | ≧0.1 | 200 | Flexible |
Dicing Saw | ≧0.1 | 200 | Straight |
Typical values. Product specifications can be adjusted according to proposals.
6Assembly
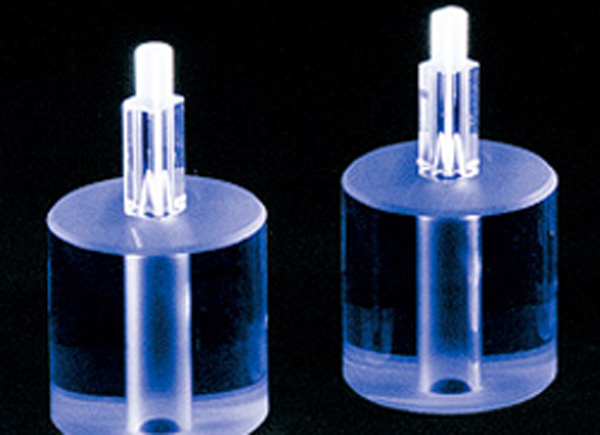
Silica glass can be formed into complex shapes by assembling multiple silica glass parts. Since the parts in these assemblies are completely integrated, these products have almost the same characteristics as the silica glass material itself. There are several preconditions for assembling silica glass.
First, the silica glass must be processed at temperatures exceeding 1,000°C. Second, there needs to be some amount of contact area. In cases where performing these types of assembly is difficult, the materials can be assembled using certain types of glass frit or adhesives. Tosoh Quartz selects the best assembly method, taking into account the level of quality and accuracy required for the product.
Comparison of Assembly Methods
Method | Surface Distortion | Heat-resistance | Chemical Inertness |
---|---|---|---|
Furnace Fusing | ○ | ○ | ○ |
Flame Fusing | △ | ○ | ○ |
Contact with Glass Frit | ○ | △ | △ |
Contact with Adhesive | ○ | △ | △ |
7Cleaning/Inspection
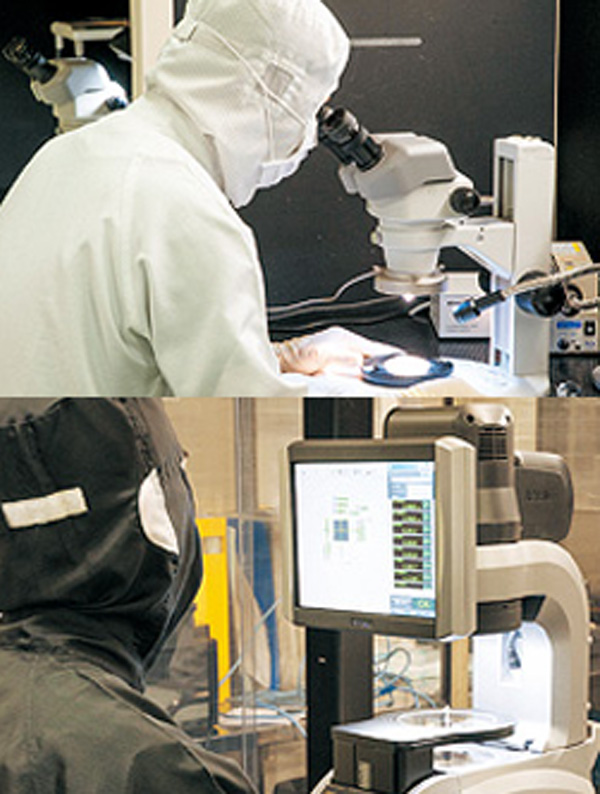
Products are cleaned in a clean-room using semiconductor photomask-level precision cleaning technology. Product quality also depends on the cleanliness of the parts. We use our own specially designed cleaning machine to clean flow cytometry cells, which are one of our major products, and have achieved a reliable level of cleanliness through an automated system for cleaning the inside channels (with sizes of 200 to 250 microns).
After being cleaned, products are inspected in a clean-room. Visual inspections by experienced inspectors are conducted by microscope. Dimensions and geometrical tolerance are measured using automated measuring devices, and all measured values are used for quality control after being compiled in a database.